Fuels
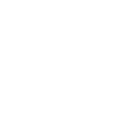
Transfer
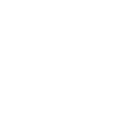
Dispense
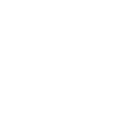
Polish
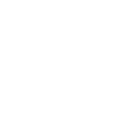
Blend
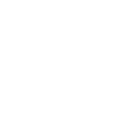
Store
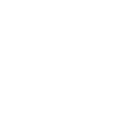
Filter
Offering Solutions for
transfer, blending, and polishing, Semler is your one-stop shop for fuel equipment.
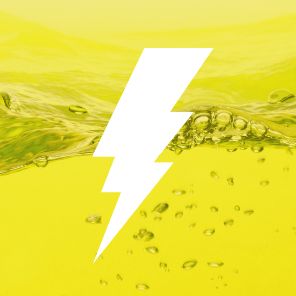
Power
generation
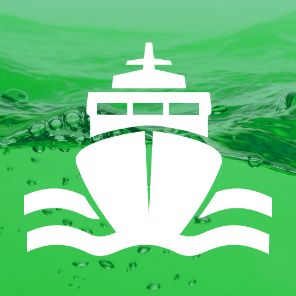
MARINE
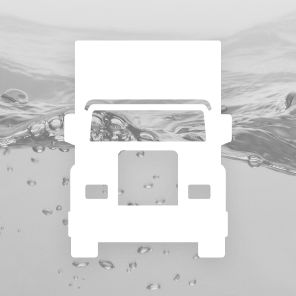
ON ROAD
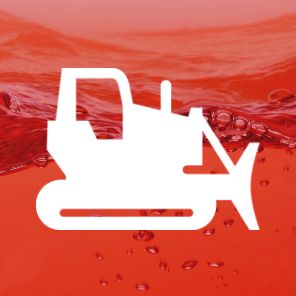
OFF ROAD
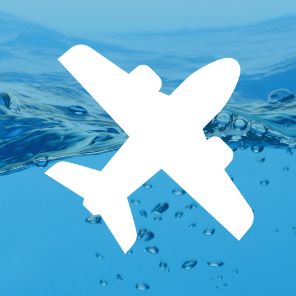
AVIATION
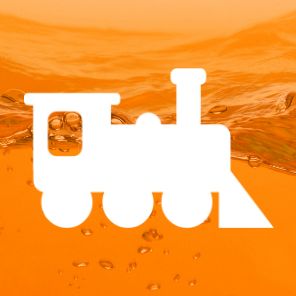
RAIL
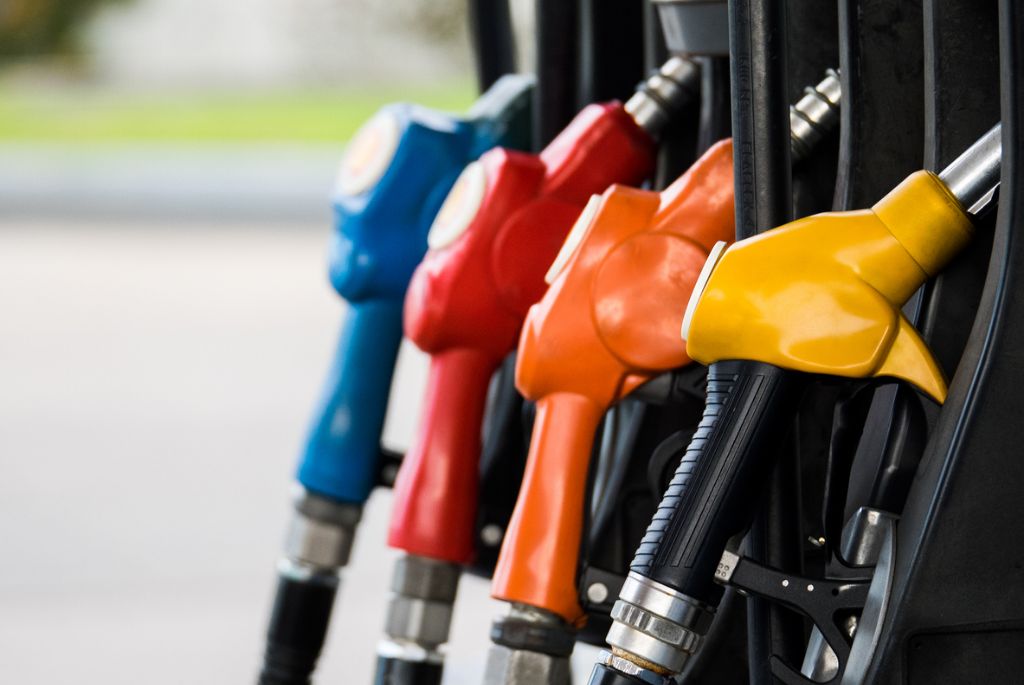
Fuels
Semler Industries has been at the forefront of fuel supply infrastructure solutions for over 50 years. Drawing from our extensive experience in traditional fuels like gasoline, aviation fuel, and diesel, as well as our innovative approaches to renewable fuels, our product lineup includes equipment designed for additive injection, dispensing, transferring, transloading, and blending. We are also proud to offer our cutting-edge PetroPolisher™ line, dedicated to fuel purification.
FIND A REP